Essential Insights into BMW Labor Time Estimates
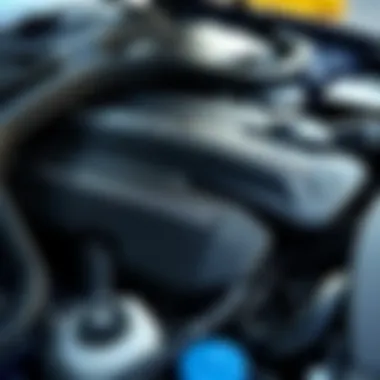
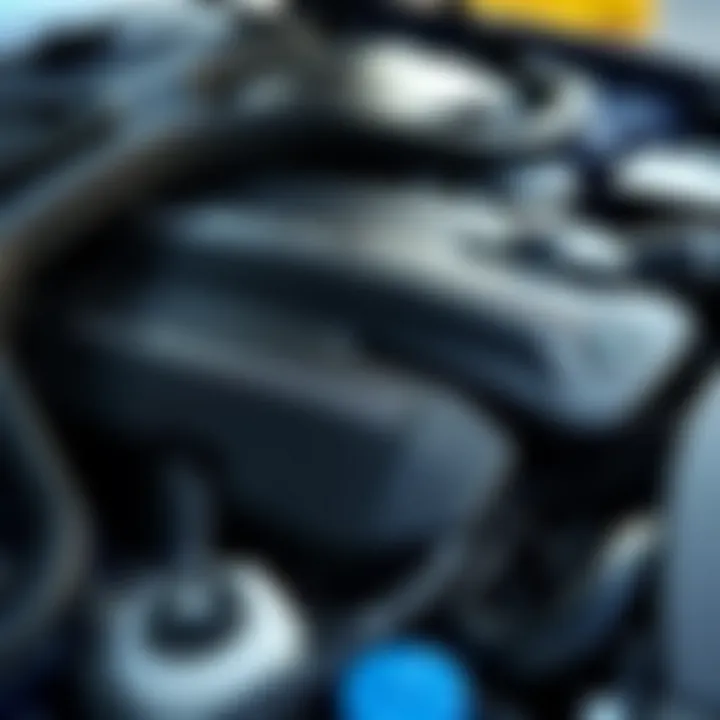
Intro
When you think of BMW, visions of engineering excellence and high-performance vehicles often come to mind. For enthusiasts, owners, and professionals within the automotive realm, understanding the mechanics that go into these machines is crucial, yet often overlooked. Labor time estimates play a pivotal role in this equation; they provide a framework for both standard practices and the unpredictable nature of vehicle repair. Knowing how long a job should take or what it entails can transform the experience of maintaining these fine automobiles.
Labor time estimates help demystify the repair process, ensuring that everyone in the automotive supply chainβfrom mechanics to customersβhas a clear understanding. Itβs like having a well-loved roadmap that saves you the trouble of getting lost when the engine misfires or that electrical system goes haywire. With the right guidance, discussing repairs, maintenance, and costs becomes less of a chore and more of a smooth conversation.
In this guide, weβll explore labor time assessments specific to BMW vehicles, touching on their significance, the methodology behind their calculation, and their practical applications in your day-to-day experiences with automotive repair and maintenance. We aim to present this information in a way thatβs straightforward yet rich in insights, particularly helpful for drivers, mechanics, and automotive salespeople.
Letβs dive into the essential aspects that will shape your understanding and help you navigate through the intricate world of BMW labor time estimates.
Understanding the BMW Labor Time Guide
Understanding the BMW Labor Time Guide is like holding the keys to unlocking the intricate workings of automotive maintenance and repair. For car enthusiasts, mechanics, and industry professionals, this guide serves as a vital tool, helping to streamline the often complex landscape of repair services. By familiarizing oneself with this guide, stakeholders can improve their approach to repairs, optimize customer satisfaction, and ultimately enhance the efficiency of their operations.
Definition and Purpose of the Labor Time Guide
The labor time guide represents a comprehensive resource that specifies the estimated hours a technician needs to complete various service tasks on BMW vehicles. This guide is essential, as it standardizes the time needed for particular repairs or maintenance tasks across different models and makes.
In a sense, it acts like a roadmap for automotive workshops. By relying on these estimates, mechanics can efficiently plan their schedules, ensuring that each job fits into the day's workload without unnecessary delays. This enhances productivity while also allowing customers to receive more accurate quotes. A well-defined labor time guide helps manage expectations for both the service provider and the customer.
How Labor Time Influences Repair Costs
Labor time is a significant factor influencing the overall repair costs that customers face. When a workshop generates a quote, it typically includes the cost of parts and the estimated labor time multiplied by the shop's hourly rate. Therefore, a job requiring more time will naturally lead to higher costs.
Unlike a flat rate, which might obscure the actual time spent on a repair, labor time estimates provide transparency. Customers can see how their charges break down, which builds trust. In essence, when a customer understands that a specific repair typically takes, say, two hours, they can rationalize the costs more easily than if they received a vague estimate.
Consider this example: if an oil change takes half an hour in the guide, the customer pays for that half an hour, not a made-up hour that doesn't accurately reflect reality. This clarity is crucial. It allows customers to plan their finances better and helps mechanics explain the reasoning behind their charges without sounding vague or dismissive.
"A well-prepared workload can transform a chaotic workshop into a well-oiled machine, where mechanics excel, and customers leave happy."
To wrap things up, itβs clear that the BMW Labor Time Guide is more than just a tool; itβs an essential framework that underpins the entire service experience, from efficiency in the shop to trust in the customer relationship. Proper understanding and utilization of this guide can lead to smoother operations and enhanced customer satisfaction.
Components of the Labor Time Guide
Understanding the components of the Labor Time Guide is crucial for anyone involved in automotive maintenance and repair, especially when it comes to BMW vehicles. This guide acts as a compass for workshops, helping to align various service expectations with realistic timelines. If youβre a driver, mechanic, or automotive salesperson, knowing these elements can not only enhance your efficiency but also improve customer satisfaction.
Types of Services Covered
The Labor Time Guide for BMW encompasses a variety of services essential to the maintenance and repair of vehicles. Typically, these include:
- Routine Maintenance: This involves oil changes, tire rotations, and brake inspections. Such basic procedures usually have standardized time estimates, which streamline scheduling.
- Major Repairs: More extensive tasks such as engine overhauls or transmission replacements demand a meticulous breakdown of labor hours. Each component of these jobs might have its own time allocation, which ensures workshops can charge accurately.
- Bodywork: Collision repairs or body modifications can vary widely in terms of labor time. Guides often categorize these estimates based on the specific model series, considering the design nuances involved in each job.
- Electrical Services: With the surge in advanced electrical features in modern BMWs, troubleshooting and repairing electronic systems necessitates both skill and time, which are captured in detailed labor hours.
By outlining these categories, BMWβs Labor Time Guide serves as a pivotal tool for both workshops and customers. It creates a transparent framework that takes the guesswork out of how long services will take, thereby fostering better planning.
Specific Models and Labor Times
In the world of automotive service, specificity is crucial. The Labor Time Guide provides detailed estimations tailored to specific BMW models, reflecting their unique service requirements. This was especially evident in models from different series:

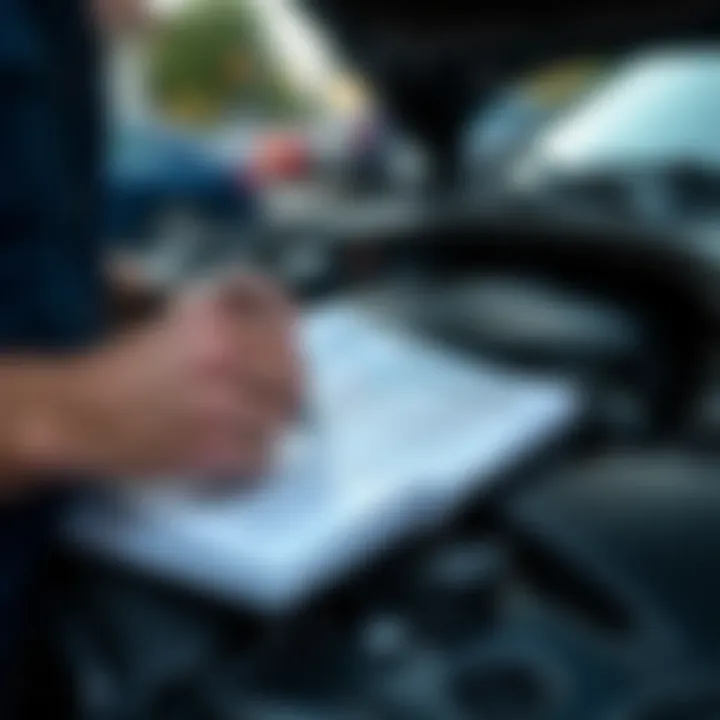
- 3 Series: Known for its sporty persona, the labor times for tasks like brake replacements might differ from the 5 Series simply due to its design and the access required to components.
- X Series: SUVs like the X5 may have labor times adjusted based on their height and weight, impacting jobs like suspension work.
- M Models: These high-performance vehicles often come with specialized services that require additional time due to their advanced engineering and performance features.
"When you work on a BMW, no two jobs are quite the same, thanks to the model specifics and trims. Having an accurate labor time estimate can make all the difference."
By offering insights on model-specific times, the Labor Time Guide helps avoid overcharging customers while ensuring technicians work efficiently within the outlined limits. Itβs sort of like having a recipe: you need the right ingredients (timing) for the dish (service) to come out just right.
Developing Accurate Labor Time Estimates
Precision in labor time estimation is pivotal for both the automotive repair industry and the stakeholders involved. A reliable estimate helps in allocating resources effectively and aligning expectations between service providers and clients. Estimating the time required for repairs plays a crucial role in controlling labor costs, which can easily spiral if not accurately predicted.
When delving into labor time estimates, it's not simply about filling in numbers on a piece of paper. It's a holistic process that encompasses various aspects of repair work. These factors range from the complexity of the job to the experience level of the technician performing the service. Therefore, having accurate labor time estimates not only aids in workflow management but also enhances customer satisfaction, leading to greater trust in the service provider.
Key Factors Influencing Estimates
Several elements come into play when developing labor time estimates for BMW repairs. Understanding these can greatly improve the reliability of the estimates:
- Type of Repair: The nature of the repair or service dictates the time required. Routine services, like oil changes, often take less time compared to complex engine repairs.
- Model Specificity: Different BMW models can demand different times due to design variations, with some models being trickier to work on than others. For instance, a repair on a BMW M series might differ significantly in the time required when compared to a standard 3 series.
- Skill and Experience of Technicians: The proficiency of the technician is another major consideration. A seasoned expert familiar with BMW intricacies will likely complete repairs faster than someone still finding their feet in the industry.
- Availability of Parts: Delays in fetching required parts can prolong repair time, potentially leading to dissatisfaction among customers. Understanding local part availability can mitigate this issue.
Methods of Data Collection
Implementing effective methods for data collection is crucial for attaining accurate labor time estimates. Mechanics and service managers often rely on:
- Historical Data Analysis: Observing the time taken for similar repair jobs in the past helps establish a baseline for future estimates. This should be regularly updated as experience accumulates, so adjustments for improved efficiencies can be made.
- Manufacturer Specifications: Referring to BMW's own guidelines and manuals provides a reliable benchmark for expected repair times on various models and services.
- Technology-Driven Tools: Utilizing software tailored for automotive repairs can streamline the estimate generation process, allowing for quicker access to labor benchmarks and reducing human error.
Incorporating diverse methods of data collection strengthens estimate accuracy. This is particularly significant in the fast-moving landscape of automotive service, where new models and technologies continuously emerge.
Expert Opinions and Industry Standards
Engaging with industry experts adds considerable value to the labor time estimation process. This process also entails:
- Consultation with Experienced Technicians: Speaking to seasoned technicians who have dealt with a breadth of repairs provides insights into what can often be underestimated.
- Adhering to Automotive Industry Standards: Following standards set by reputable organizations ensures that the labor estimates are aligned with broader industry practices, lending credibility and consistency.
- Joining Professional Networks: Engaging within automotive forums and attending industry seminars often uncovers emerging trends, allowing for adaptive labor estimation techniques.
In navigating the landscape of labor time estimates, an investment in ongoing education and collaboration is key. Personal approaches and adherence to established norms merge to create a foundation where accuracy thrives, ultimately benefiting the business and its clientele.
Practical Applications of Labor Time Estimates
In the realm of automotive service, labor time estimates serve as a vital cog in the machinery of repair and maintenance. For BMW owners and service providers alike, understanding how these estimates are put into action can make a world of difference in terms of efficiency and customer satisfaction. Labor time estimates provide a framework that not only influences scheduling but also impacts communication between mechanics and customers. They shape expectations and ultimately drive the daily operations of repair shops. A well-structured approach can help mitigate misunderstandings and enhance the service experience.
Service Scheduling and Efficiency
When it comes to keeping a workshop running like a well-oiled machine, practical applications of labor time estimates are indispensable. Think about it: every minute counts in a service department. By having a clear understanding of how long each task will take, workshops can allocate resources effectively.
Consider these benefits of accurate scheduling:
- Enhanced Efficiency: By knowing the standard time for a service or repair on a BMW, mechanics can optimize workflow. They can tackle jobs in a logical order, avoiding the pitfalls of overbooking or underestimating capacities.
- Reduced Wait Times: Clients hate waiting around. With precise estimates, service advisors can set realistic timeframes for completion, allowing vehicles to be serviced within those frames. This results in a smoother customer experience.
- Better Resource Allocation: Knowing labor times allows workshops to plan for busy days. They can ensure they have enough experienced staff on deck, without necessarily overstaffing during quieter periods.
Like trying to fit a square peg into a round hole, mismanaging time can lead to chaos in the workshop. Labor time estimates help ensure that every bit of effort put forth is worthwhile.
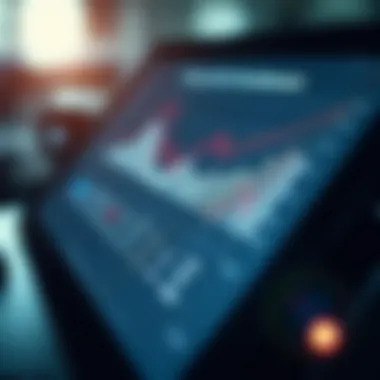
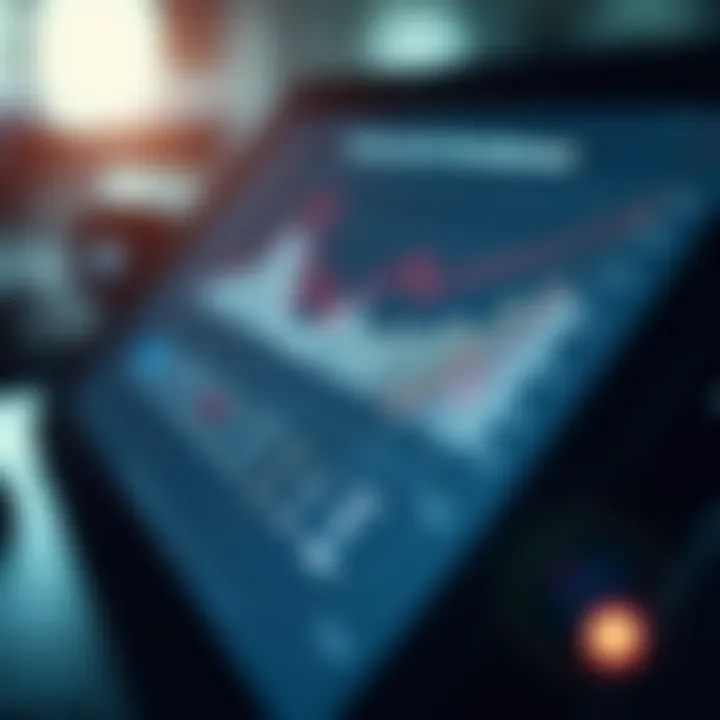
Customer Communication and Transparency
Labor time estimates also play a significant role in the communication dynamics between service personnel and customers. Imagine walking into a BMW service center with little to no idea about what your repair entails. It can be confusing, maybe even intimidating. Thatβs where transparency steps in.
Here are key aspects of how labor time estimates improve communication:
- Clear Expectations: Providing customers with time estimates gives them a concrete understanding of what to expect. They can plan their day accordingly, whether it means waiting at the shop or arranging alternative transportation.
- Strengthening Trust: When service centers use established labor time guides, they showcase a level of professionalism and transparency. Customers are more likely to trust mechanics when they provide logical timeframes backed by standardized labor estimates.
- Room for Discussion: When a job takes longer than estimated, having an upfront discussion about expectations allows for better customer relations. It becomes easier to explain any complications that arise during the repair process, maintaining a positive relationship even amid delays.
Challenges in Labor Time Estimation
In the realm of automotive repair, estimating labor time is akin to trying to predict the weather; it can often feel unpredictable and subject to a variety of changing factors. Understanding the challenges associated with labor time estimation is crucial for workshops, mechanics, and customers alike. The core of these challenges often lies in the rapid evolution of vehicle technology, the myriad of unique repair situations that arise, and a constant tug-of-war between the speed of repairs and the quality of service provided.
Changes in Vehicle Technology
As technology in vehicles progresses, more intricate systems and components emerge that require specialized knowledge and skill sets. Take, for instance, the rise of electric and hybrid vehicles. These models come equipped with complex electronic systems and high-voltage batteries, contrasting sharply with the traditional internal combustion engines. Mechanics can no longer rely solely on past experiences; they must adapt quickly to new diagnostic tools and methods, which adds layers of unpredictability to labor time estimates.
Moreover, features like advanced driver assistance systems (ADAS) have added another dimension. Repairs on components like radar sensors or camera calibration can involve extensive timeframes simply because the technology demands precision. In this context, one canβt help but wonder how a mere mechanical shortcut could lead to overestimating or underestimating time frames!
Variability in Repair Situations
Each vehicle repair scenario is unique. What might seem like a straightforward task on a BMW 3 Series could turn into a can of worms on a 5 Series, depending on various factors like service history, the condition of used components, or even previous repair attempts. Repair situations can vary not only between models but also between individual vehicles due to how they have been maintained or run.
Unfortunately, even seasoned mechanics may find themselves stuck when unexpected issues crop up during the repair. For example, a mechanic might open up a car to find rust on components that were not visible prior to the job, now forcing them to rethink their labor time estimate. Thus, flexibility becomes essential in estimating labor times; they should reflect not just the planned work, but also the potential for surprises beneath the surface.
Balancing Speed and Quality of Service
The automotive industry often pressures workshops into a high-octane race against time to meet customer demands while ensuring top-notch quality. Striking the right balance can be a daunting task. If a workshop seeks to boost its turnover by promising swift repairs, it might inadvertently compromise on the quality of service, leading to dissatisfied customers who seek resolution elsewhere. This is a slippery slope, as gaining a reputation for hasty work can drive away repeat customers, ultimately affecting the bottom line.
To mitigate this, many shops employ a two-prong approach: invest in training for staff on new technologies and ensure a realistic view of how long repairs will take. The emphasis on training, in particular, can help mechanics adapt to the changing landscape of automotive repair, enabling them to work at a steadier pace without sacrificing quality.
It's not just about time saved; it's about doing the job right the first time.
In essence, the challenges in labor time estimation revolve around adaptability and foresight. Keeping a close eye on technological advancements, acknowledging the unique nature of each repair task, and finding a harmonious balance between speed and quality can all contribute significantly toward creating reliable labor time estimates. Addressing these challenges not only enhances the service provided by workshops but also fosters trust between consumers and service providers, setting the stage for smoother automotive repair experiences.
Impact of Labor Time Guides on the Automotive Industry
Labor time guides are more than just numbers on a page; they're a crucial part of the automotive ecosystem, affecting every layer from the workshop floor to the end consumer. In the case of BMW, these guides help streamline processes, provide transparency, and influence customer satisfaction. With a clear understanding of labor time estimates, workshops can operate more efficiently and customers can feel more confident about their investment in repairs and services.
Economic Implications for Workshops
A workshopβs profitability hinges on the accuracy of its labor time estimates. When these estimates are drawn from reliable guides, it becomes easier for workshops to set competitive pricing without leaving money on the table. Accurate labor time guides help them to:
- Predict Revenue: Knowing how long a job should take allows for proper scheduling and better financial forecasting.
- Optimize Workflow: By having a reliable time frame, mechanics can juggle multiple jobs more efficiently, ensuring no wasted effort.
- Reduce Disputes: Clear estimates minimize the chances of disagreements with customers over service times and costs.
However, if a workshop relies on outdated or inaccurate guides, it can lead to over or underestimating the time needed for repairs. This ultimately affects their bottom line and reputation.
"Accurate estimates, in essence, are the backbone of effective pricing strategy and customer satisfaction in the automotive repair industry."
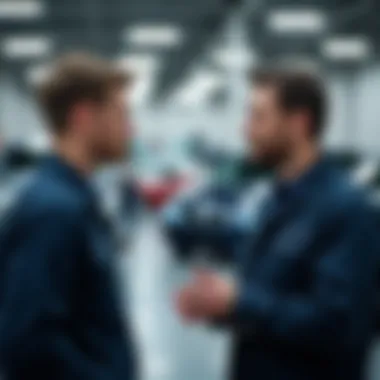
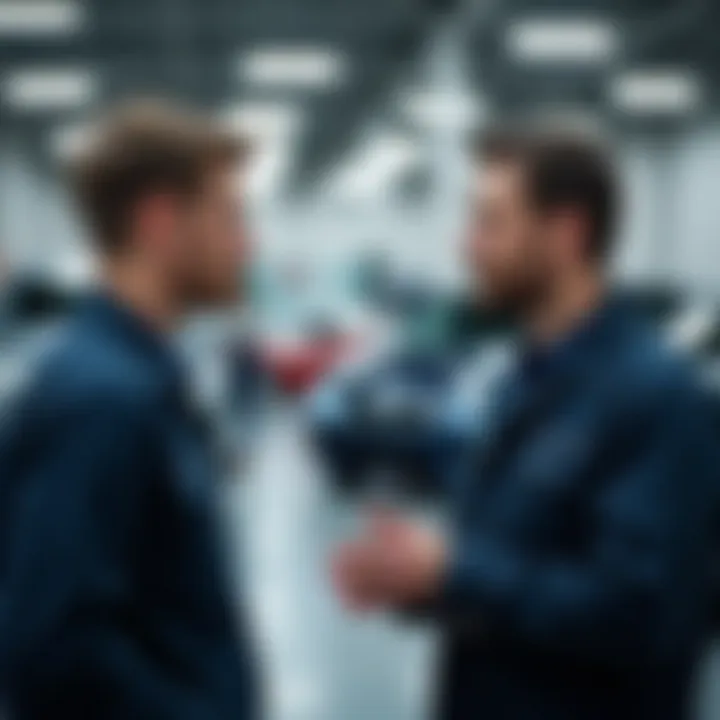
Effects on Consumer Trust and Loyalty
For customers, transparency in service is akin to a breath of fresh air. When they can see a detailed breakdown of labor times, it creates a sense of trust that is invaluable. Factors contributing to this trust include:
- Clarity: Customers appreciate upfront estimates that are grounded in formal guides. They can compare these estimates against actual service times and costs.
- Consistency: When a workshop regularly uses reputable labor time guides, customers begin to develop loyalty as they know what to expect in terms of pricing and service time.
- Quality Assurance: Knowing that a workshop adheres to established benchmarks adds confidence, making customers more willing to return time and again.
Having reliable labor time estimates can foster trust between customers and automotive workshops, enabling a more loyal client base. Overall, the influence of labor time guides in the industry cannot be overstated; when used effectively, they not only enhance operational efficiency but also bolster consumer relationships.
The Future of Labor Time Estimation
With the automotive industry rapidly evolving, the future of labor time estimation is a topic ripe for exploration. As vehicles become increasingly complex, understanding how to effectively estimate labor hours will be crucial for both repair workshops and consumers. The growing integration of technology fuels changes in the repair and maintenance landscape, affecting everything from timeliness to cost precision.
Emerging Technologies in Automotive Repair
Automotive repair is on the brink of a technologic revolution, significantly impacting how labor time is estimated. Innovations in diagnostics, such as advanced scanning tools, can enhance accuracy and efficiency in determining repair needs. For instance, instead of manual input or outdated methods, technicians can use devices that instantly communicate fault codes and recommend repairs. This immediacy in diagnosis narrows the gap between service expectation and delivery, streamlining the repair process.
Moreover, augmented reality (AR) is making inroads into the training of technicians. With virtual overlays that guide mechanics through complex repairs, the learning curve shrinks. Not only does this method boost confidence among less experienced technicians, but it also ensures that repairs are completed within anticipated time frames. As a ripple effect, workshops can better manage their schedules and potentially offer more competitive pricing to customers.
Key advancements include:
- Telematics: Real-time vehicle monitoring helps anticipate repairs before issues escalate, reducing unnecessary labor time.
- 3D Printing: On-site production of parts can cut down waiting times drastically, thereby affecting labor estimates positively.
- Robotics: Automated systems can handle repetitive tasks, letting skilled technicians focus on more complex solutions.
These technologies promise to refine labor time estimates, ensuring they reflect true service needs rather than arbitrary calculations.
Integrating AI and Machine Learning
Artificial Intelligence (AI) and Machine Learning are set to redefine labor time estimation fundamentally. By analyzing vast amounts of data, AI systems can predict labor times based on numerous variables, including vehicle type, past repair histories, and even technician expertise. This data-driven approach allows for more personalized and accurate estimations.
Consider the implications for a workshop that typically services several BMW models. By harnessing AI, they could analyze previous repair jobs and quickly formulate a database that suggests labor times for specific repairs. If a technician is well-versed in working on, say, a BMW M3, the system can automatically adjust labor estimates according to their known efficiency and past performance rates.
- Predictive Analytics: This feature ensures that workshops can not only provide accurate labor estimates but also anticipate potential bottlenecks and adjust service schedules accordingly.
- Customer Relationship Management (CRM) Integration: AI tools can help manage customer interactions more effectively by providing transparent labor time estimates, aligning customer expectations with actual service capabilities.
"With AI and machine learning, the accuracy of labor time estimates will shift from best guesses to informed predictions based on historical trends and analysis."
In summary, as emerging technologies and AI converge, the automotive repair sector stands on the cusp of transforming labor time estimation into a more refined art. This future holds promises of improved service quality, heightened customer satisfaction, and a more balanced workshop workload.
Finale
In summing up the discussion on BMW labor time estimates, itβs clear that precision in these estimates is crucial, not just for automotive technicians but for anyone involved in the automotive field. Understanding labor time not only leads to better customer experiences but also offers workshops and technicians a clearer pathway to maximize efficiency. The ability to accurately gauge how long a job will take can save money, time, and resources across the board.
Summary of Key Takeaways
- Understanding Estimates: Knowing the labor time required for different services helps provide clearer quotes and improves customer trust.
- Practical Implications: Accurate estimates can streamline service scheduling, ensuring that mechanics can work on cars without unnecessary delays. This leads to a smoother workflow inside the garage.
- Competitive Edge: Accurate labor time calculations can give workshops an advantage in a competitive market. Businesses that demonstrate transparency in costs tend to foster customer loyalty.
- Training and Knowledge: Staff training related to labor time estimation means fewer misunderstandings with clients and sets realistic expectations for both sides.
Final Thoughts on the Importance of Accurate Estimates
When it comes down to it, the significance of accurate labor time estimates in the automotive realm cannot be overstated. In a world where customer satisfaction frequently determines success, mechanics and service centers must grasp the nuances involved in estimating repair times. Misinformation can lead to unhappy clients, lost revenue, and a tarnished reputation.
Moreover, as vehicles integrate more advanced technology, the complexity of repairs increases, making it necessary for technicians to stay ahead of the curve. Keeping abreast of industry standards and ongoing education will only enhance labor time estimates and improve service quality. The truth is, in this line of work, knowledge is power. By properly leveraging labor time estimates, every involved party can create a smoother, more profitable, and more trustworthy experience in automotive care.
"In the auto repair business, time is literally money. Every minute counts, and accurate estimates can make all the difference."
This encapsulates the essence of why accurate labor time estimates in BMW repair and maintenance are so vital, tying the entire guide together with a practical lens.